NoticiasPortada
La tecnología de fusión por láser aditivo.
Los avances tecnológicos permiten a la industria alcanzar logros que antes parecían imposibles, permitiendo realizar desarrollos cuyos beneficios están dirigidos a aportar evolución en el desempeño técnico al utilizar la tecnología de impresión en 3D para diseñar piezas de alta complejidad, amalgamando características importantes tales como menor peso, mayor rigidez, rapidez de construcción y sobre todo optimización en el diseño.
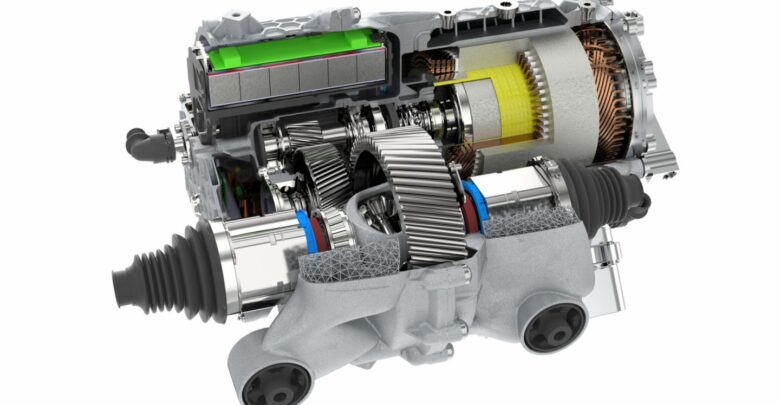
Para interpretar lo recién mencionado, quiero resaltar la importancia que tiene la tecnología de impresión en 3 dimensiones (3D), donde previamente se desarrolla digitalmente la pieza a fabricar en un ordenador para luego realizarla mediante el uso de una impresora 3D, mediante el aporte del láser aditivo que va fusionando material a través de capas. El objetivo central pasa por optimizar la construcción de piezas que revisten cierta complejidad en sus formas, y que a su vez facilita la optimización en la manufactura de determinados sistemas como puede ser la incorporación de la canalización del sistema de lubricación en las paredes de la pieza a construir. Si bien actualmente la utilización de esta tecnología no está implementada masivamente, algunas marcas hacen uso de esta gran herramienta para poder amalgamar sistemas que actualmente empiezan a tener cierta complejidad a la hora de mejorar la funcionalidad, como puede ser el caso de integrar un motor eléctrico en una caja de cambios. En esta dirección, la empresa Porsche comenzó la fabricación de una carcasa de aleación que agrupa varias funciones e involucra piezas de sistemas diferentes que se complementan en una misma tarea. En este orden de descripción, Porsche hace uso del proceso de fusión de material de aleación mediante la utilización del láser aditivo, el cual posibilita obtener piezas que son mucho más livianas de peso, incrementan la rigidez estructural y logran un producto de alta calidad. De esta manera Porsche optimiza la construcción de piezas que están sometidas a grandes esfuerzos. Básicamente el procedimiento para la fabricación de esta carcasa de aleación de aluminio se da inicio al cargar en el ordenador los datos del diseño de la pieza a construir, y se le envían a la impresora los datos que necesita sin intervención de ninguna otra herramienta intermedia.
Paso siguiente comienza la producción en sí, al crear capa por capa mediante el aporte del polvo de aleación de aluminio de alta pureza que va delineando las paredes de la pieza, incluyendo de acuerdo al diseño, los conductos integrados encargados de la refrigeración independientemente de la geometría de la misma. Este método se lleva a cabo dado que el rayo láser calienta y termina fundiendo la superficie de la capa del polvo de material de alta pureza aportado, permitiendo fusionarla con la capa anterior, formando de esta manera el volumen y delineando la figura definitiva diseñada en el ordenador. En esencia este es básicamente el procedimiento, pese a que hay algunas tecnologías similares. Este proceso de fusión de metales por láser (denominado LMF), permite lograr piezas que en un principio aligera su peso en un valor promedio al 40%: este dato no pasa para nada desapercibido, ya que más allá de este logro, se pudo comprobar que prácticamente se ha duplicado la rigidez estructural en las zonas a las que es sometida a lo que se denomina estrés por carga. Por otro lado, la construcción en una sola pieza facilita la integración de muchas piezas y funciones, disminuyendo sensiblemente la operación de montaje. Este concepto de integración mejora significativamente el volumen necesario para adaptar los sistemas, logrando un diseño más compacto. Muchos beneficios he mencionado hasta ahora, sin mencionar que la optimización de procedimientos y mejora en la tecnología alcanzada por las impresoras de 3D, facilita la producción de la pieza definitiva en tan sólo 20 minutos en un solo proceso.
Este desafío permitió desarrollar un producto con menos operación de montaje, menor peso, mayor resistencia y rigidez estructural, permitiendo incorporar sistemas que se puedan complementar. Todo un logro. Ahora bien, Porsche ya había echado mano de esta tecnología para la fabricación de los pistones que fueron utilizados en el 911 GT2 RS, cosa que demuestra que los vehículos de alto rendimiento salen favorecidos ampliamente con este aporte tecnológico. Me resta mencionar, que el uso de esta tecnología de construcción no es aplicable ni rentable para grandes escalas, pero por el contrario sí puede ser interesante para alcanzar metas muy específicas orientadas al diseño de piezas que reflejen un esfuerzo direccionado en pequeño volumen de producción y sobre todo a la optimización en el ámbito de la competición.